Solutions
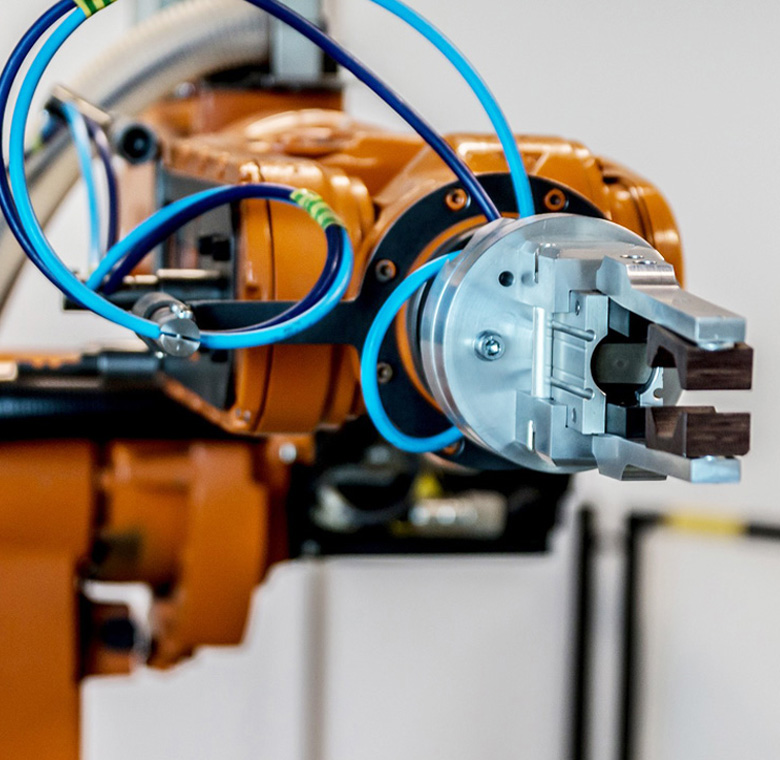
What is Machine Vision?
Machine vision is the technology and methods used to provide camera or vision sensor based automatic inspection and analysis for applications in different industry. Machine vision uses different image processing softwares and hardwares. It attempts to integrate existing technologies in new ways and apply them to solve real world problems. The term is the prevalent one for these functions in industrial automation environments.
What type of solutions do we provide?
In present scenario, Manufacturing industries are going in for automation due to shortage of skilled manpower, restrictions on compliance mechanisms, high raw material costs and expectation of high quality from consumers. Due to this various industries are considering automation of more jobs to meet the above requirements.
In the food industry, where margins are slim, machine vision based automation continues to make inroads in efforts to increase competitiveness through improved efficiency, productivity, and cost savings. We provide solutions in Food industries for machine vision based automation.
Where do you find automation in the food industry?
Automation can be found in every phase of food harvesting, processing, preparation, and transportation.
Fast food restaurants leverage automation to create efficiency and improve productivity for everything from flipping hamburgers to frying chicken. Older automation merely helped workers by alerting them for cook times and temperatures. Improvements in robotics and sensors have made it possible to use machinery to take over more of the manual labor.
Innovations like smart ovens can combine several appliances like a convection oven, dehydrator, air fryer, warming drawer, broiler, slow cooker, and toaster. Smart ovens can even have cameras inside for monitoring food as well as remote activation and even automatic temperature setting based on what’s placed inside of it.
Food processing plants and warehouses are using more automatic guided vehicles for transporting raw materials and finished products in place of forklifts. These vehicles have reduced product damage and reinforced workforce discipline.
Modern food processing and packaging continues to add automated ovens, cutting and forming machines, mixers and blenders, sorting equipment, filling and wrapping equipment, and other machinery to the assembly line. Instead of sitting at the line, workers stay in a control room to ensure everything continues to flow smoothly, make modifications in processes, and troubleshoot problems.
Even grocery stores are getting into the game, using automated machinery to pick and fill e-commerce orders in their warehouses. Now days more of automation is done in the production based food industries.
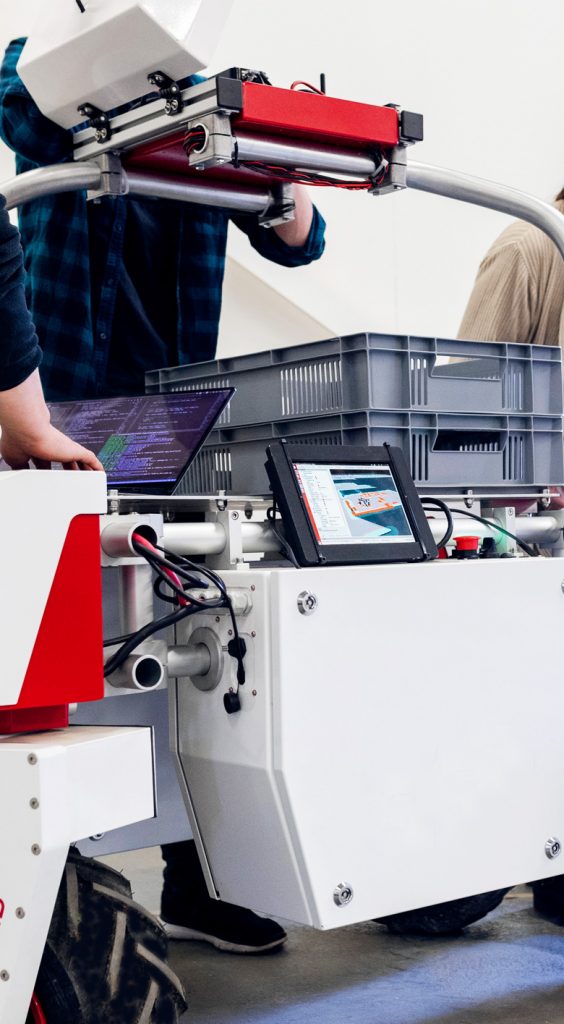
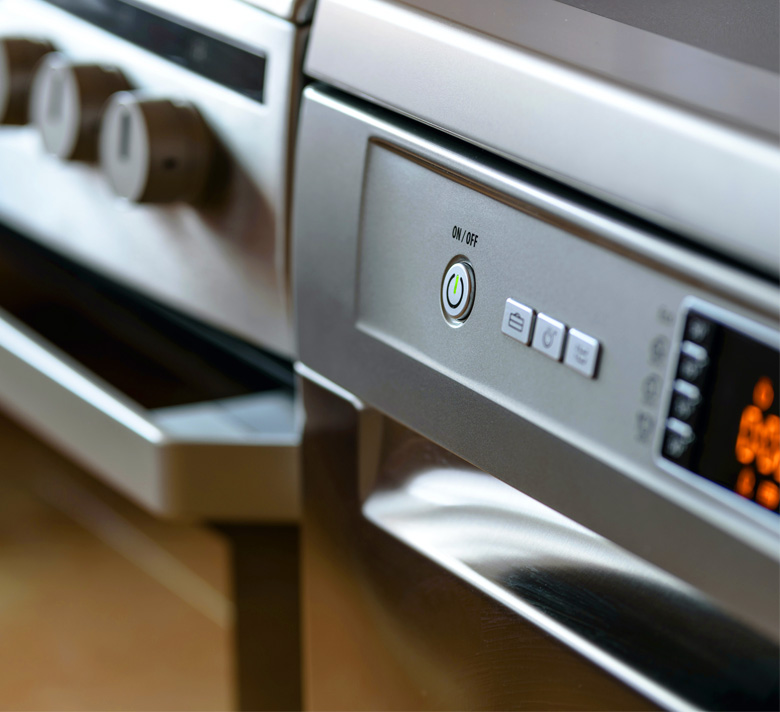
What are the considerations for selecting automation?
Hygienic design and strategic inventory planning are two areas to keep top of mind when selecting automation in food manufacturing.
Meeting FSSAI safeguards require machinery with specific characteristics such as impervious surface finishes, non-corrosive parts, no cracks or crevices, toxin-free materials, and high durability. Everything from conveyor belts to stuffers must maintain hygienic standards.
Going back to the ever-shifting consumer, the ability to implement lightweight and flexible technology can help determine inventory needs without shortages or excess materials.
Automation in the food industry increases competitiveness by eliminating errors and waste, improving efficiency and productivity, and expanding profit margins. Cost savings can be diverted to R&D and other business improvements. Businesses can keep up with regulatory changes with less effort, decrease labor costs, and eliminate injury.
Our solutions
Food Automation Market by Application
- Packaging and Repacking
- Palletizing
- Grading and Sorting
- Pick and Place
- Processing
- Others
Food Automation Market by Industry Verticals
- Beverages and Distilleries
- Dairy Processing
- Bakery and Confectionery
- Meat, Poultry, and Seafood Products
- Meat, Poultry, and Seafood Products
- Fruits and Vegetables
- Others
Case studies
Packaging
In food industry packaging is very important; we provide solution to meet the customer's requirements. We design solution to overcome customer's problem by means of Machine vision based automation. Different Barcode and text types can be read. The types are as follows CODE128, ECC200, EAN/GTIN, GS1 and QR. For further other type of OCR reading please contact us.
Casestudy
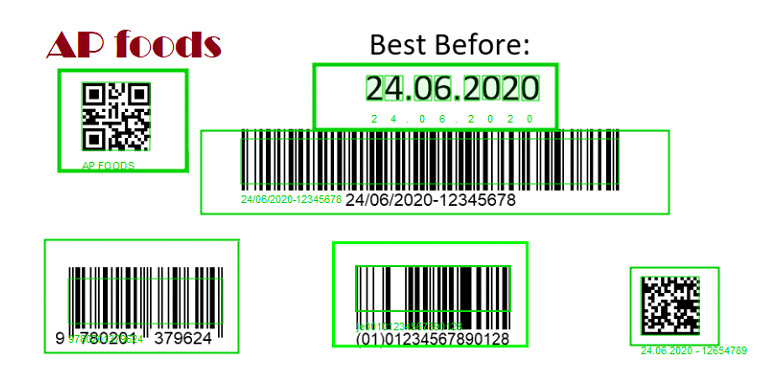
Different types of OCR reading
Print quality testing
Print quality is very important because OCR detection cannot be carried out if the print is bad. To overcome this we provide print quality testing if the product is printed with industrial standards.
Casestudy
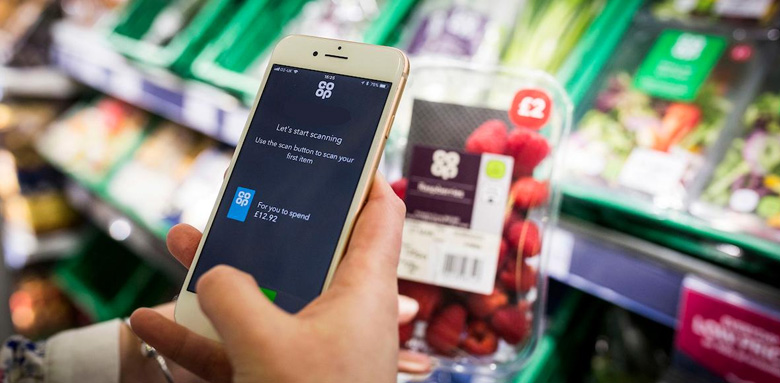
Best quality OCR detection
Sorting
To provide good quality of food product to the end user the bad food and good food product have to be sorted. Sorting can be done in many ways. We provide solutions for sorting of food product by means of shape.
Casestudy
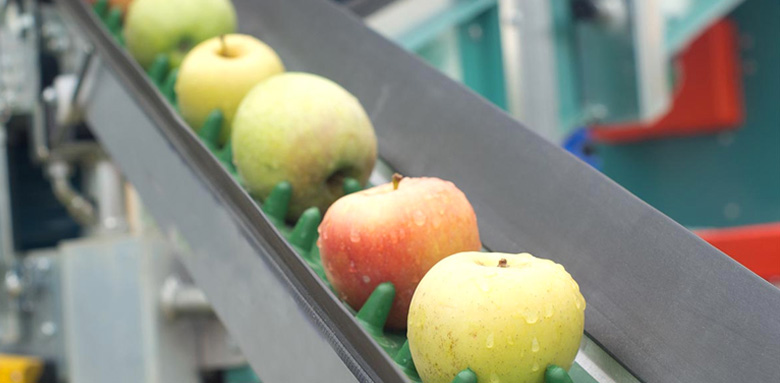
Good quality food product sorting
Quality testing
Quality is more important for any production industry. Quality testing plays a vital role in production industry. With reduced man power, reduce manual failures, reducing production to wastage ratio Machine vision based industrial automation plays a vital role in production industries.
Casestudy
In this case study bottle cap are detected and found if they are sealed. This method of automation avoids spilling of food products.
Casestudy
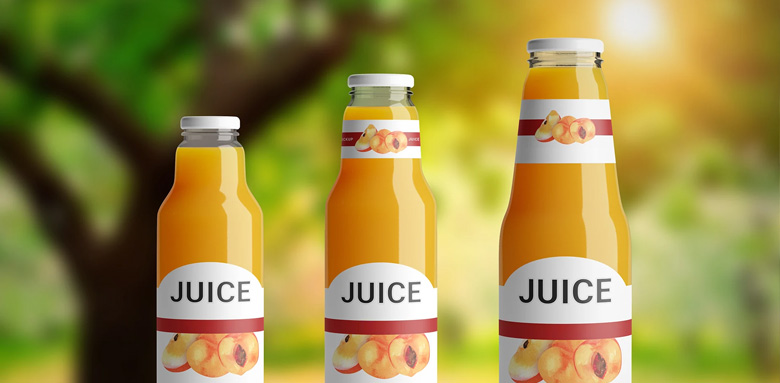
Bottle cap detection
Advantages of Machine Vision based automation
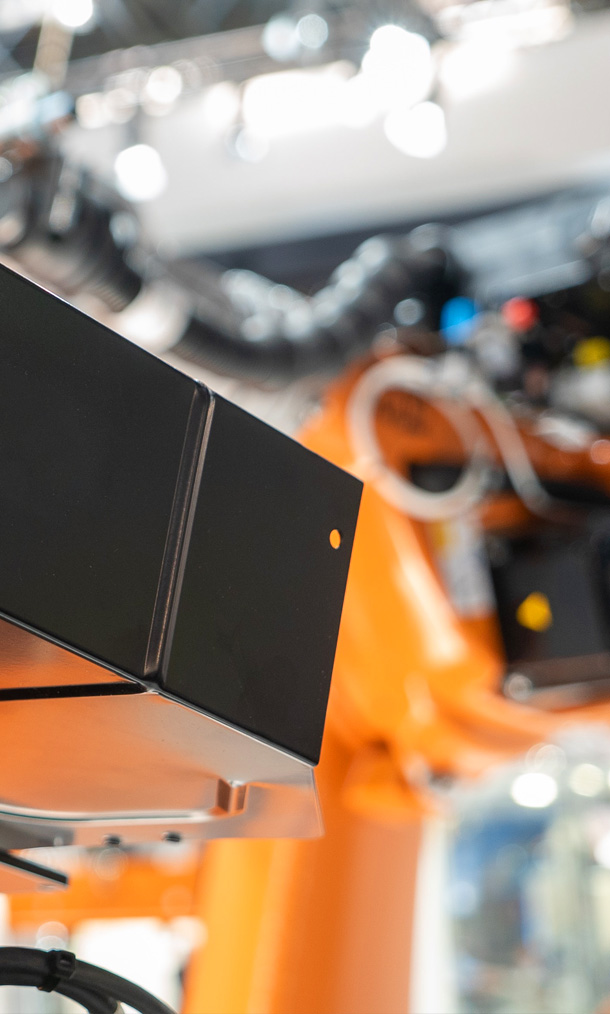
Consistent Quality
The implementation of modern technology is inevitable when it comes to producing high-quality products consistently. Automated processing and packaging gives operator greater control over consistency, which means a producer, can deliver quality products time after time. Since automation makes it easy to monitor equipment performance parameters, the process to locate and resolve issues becomes hazard-freThe implementation of modern technology is inevitable when it comes to producing high-quality products consistently. Automated processing and packaging gives operator greater control over consistency, which means a producer, can deliver quality products time after time. Since automation makes it easy to monitor equipment performance parameters, the process to locate and resolve issues becomes hazard-free.
Improved traceability
The element of traceability has gained considerable attention as it allows quickly recalling products and tracking production. It is important to trace the history of products at any stage in the chain and to track down product information: raw material intake, packaging data, processing procedures, distributions channels, etc. By adopting automation and streamlining traceability, a manufacturer can cut down on regulatory compliance costs and improve key operations.
Improved safety
When machine vision and automated systems work together, managers get a more granular view of every step in the process. The process to modify safety standards becomes smooth as a change in one process does not affect other areas.
Conclusively speaking, automation brings about safety, error-free production, transparency, and consistent quality which are critical to maintaining a brand’s good reputation and keeping both consumer and retailer satisfied. If you are still relying on manual food processing, it’s high time to implement automation and improve your bottom line.
Quick Contact
Please let us know if you have a question, want to leave a comment, or would like further information about Kalpavrükshā Solutions.